Silicone Manufacturing Technologies: HCR, LSR, and Extrusion
Silicone is one of the most versatile and durable materials, widely used in industries such as medical, automotive, electronics, and consumer goods. However, not all silicone products are made using the same process. The three main manufacturing technologies for silicone products are HCR (High Consistency Rubber), LSR (Liquid Silicone Rubber), and Extrusion. Let’s explore the differences between these technologies and their applications.
HCR (High Consistency Rubber)-Soild Silicone Rubber
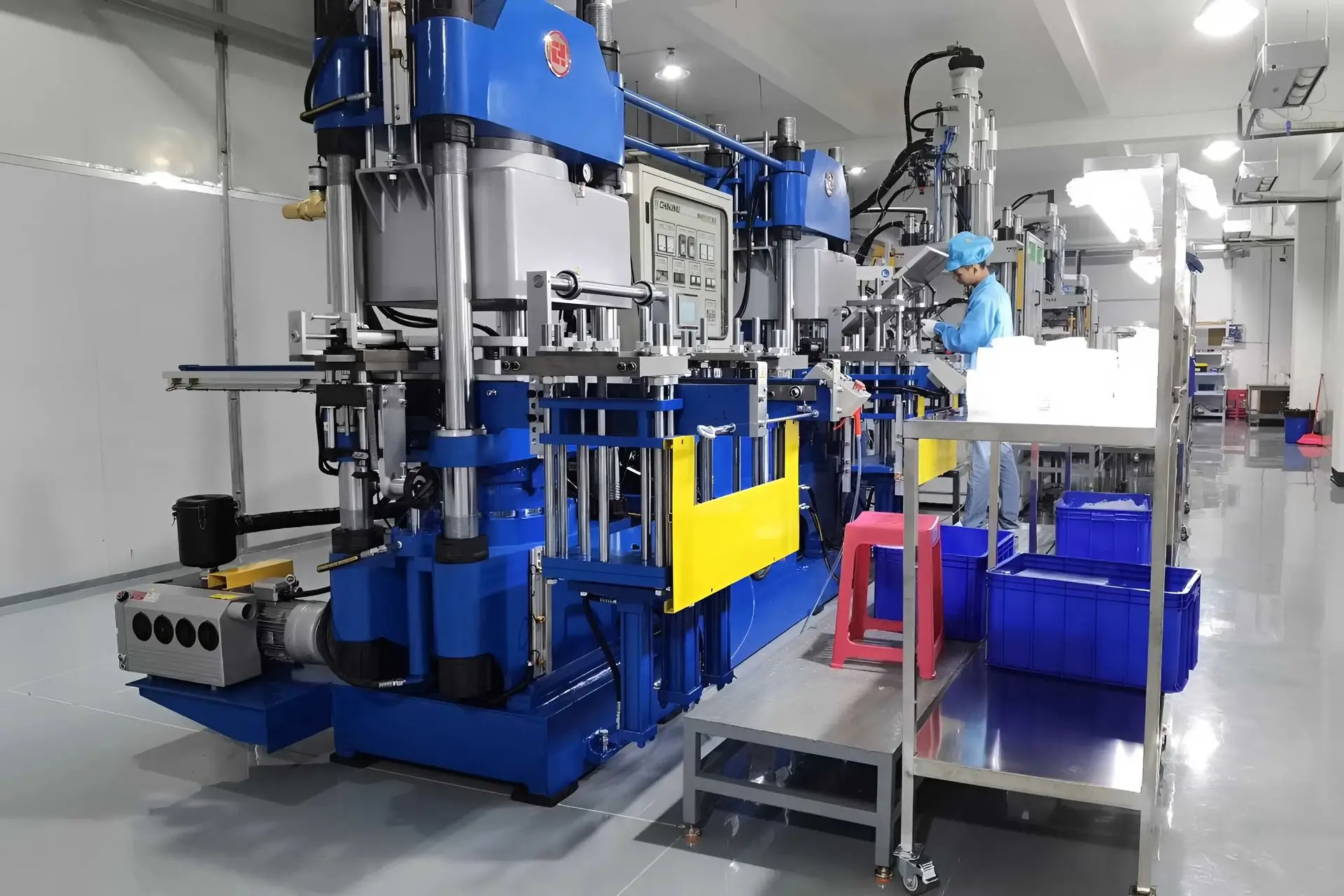
HCR is a high-viscosity silicone material, often referred to as solid silicone rubber. It has properties similar to traditional rubber but with superior heat resistance, elasticity, and chemical resistance.
HCR Manufacturing Process
- HCR is typically supplied as raw silicone material that needs to be mixed with a curing agent before shaping.
- The most common manufacturing methods are Compression Molding and Transfer Molding.
- After molding, the product is cured at high temperatures to achieve the desired hardness and mechanical properties.
Advantages of HCR | Applications of HCR
|
✅ Excellent heat and chemical resistance. ✅ Suitable for producing large, durable parts. ✅ Easily customizable in hardness and color.
| ✔️ Automotive components such as seals and air ducts. ✔️ Medical devices like catheters and pacifier nipples. ✔️ Household items such as baking molds and heat-resistant mats.
|
LSR (Liquid Silicone Rubber) - Liquid Silicone Rubber
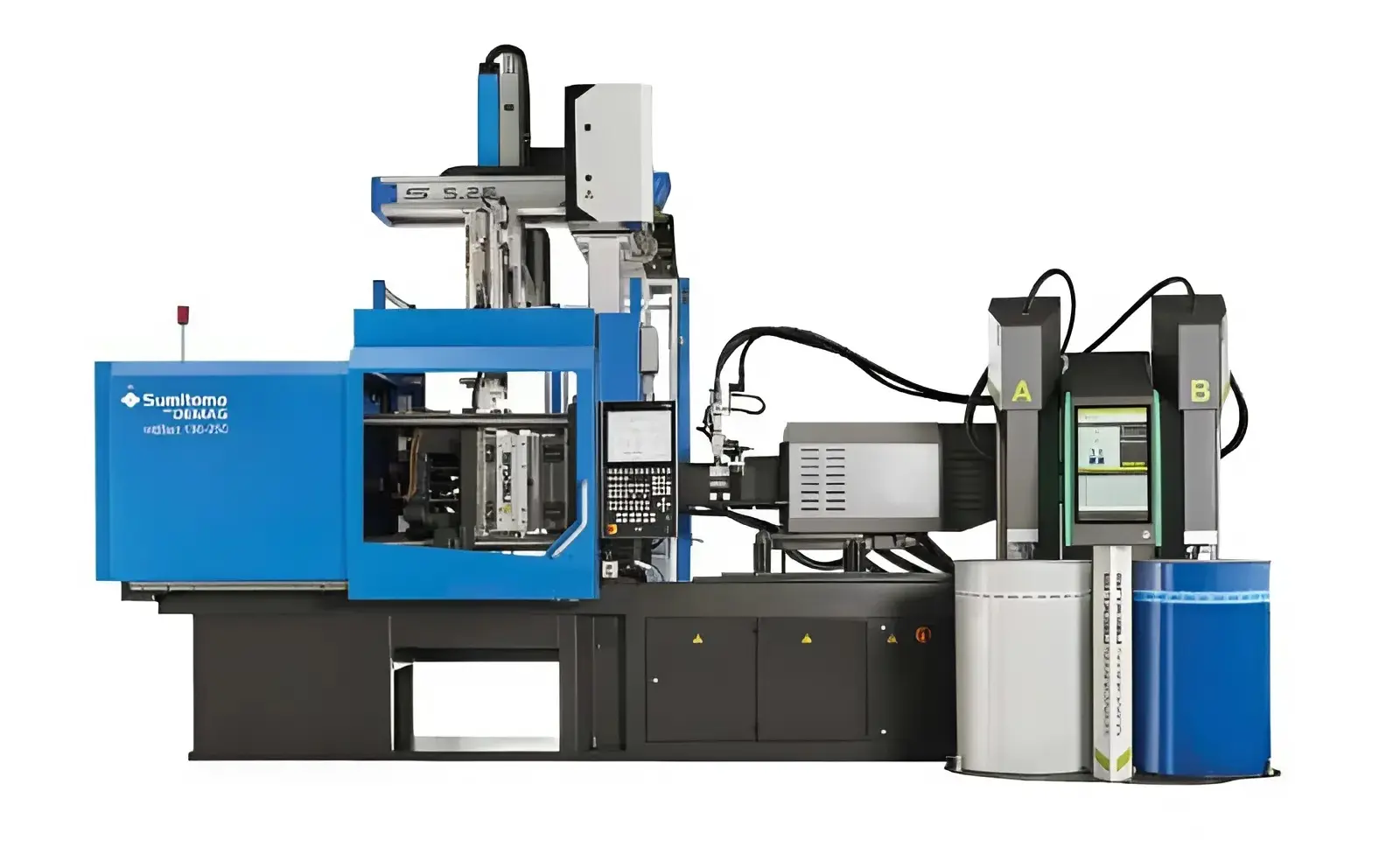
LSR is a low-viscosity silicone material in liquid form, allowing for high-precision, fully automated production.
LSR Manufacturing Process
- LSR consists of two components (A and B) that are mixed and injected into a mold using Injection Molding.
- The injection process takes place in a closed system, ensuring high precision and minimal defects.
- The molded product is cured rapidly, usually within seconds or minutes.
Advantages of LSR | Applications of LSR |
✅ Highly automated, reducing labor costs. ✅ Ideal for mass production with extreme precision. ✅ Safe for medical applications, free from impurities
| ✔️ Medical devices like syringes and baby bottle nipples. ✔️ Electronic components such as keypads and gaskets. ✔️ Automotive lighting and high-temperature-resistant parts |
Extrusion - Silicone Extrusion Technology
Extrusion is a common method for manufacturing continuous silicone products such as tubes, seals, and gaskets.
Extrusion Manufacturing Process
- Silicone (usually HCR) is fed into an extrusion machine.
- The material is compressed and pushed through a die to form the desired shape.
- The extruded product is then cured using heat or steam to achieve durability and elasticity.
Advantages of Extrusion | Applications of Extrusion |
✅ Ideal for producing long, continuous silicone products. ✅ Lower production costs compared to injection molding. ✅ Can be reinforced with additional layers for extra durability
| ✔️ Medical and food-grade tubing. ✔️ Automotive door seals and refrigerator gaskets. ✔️ Heat-resistant silicone belts and profiles
|
Comparison of HCR, LSR, and Extrusion
Technology | Key Characteristics | Advantages | Typical Applications |
HCR (Solid Silicone Rubber) | High viscosity, requires curing | Durable, heat-resistant, easy customization | Seals, automotive parts, medical products |
LSR (Liquid Silicone Rubber) | Low viscosity, injection molding | High precision, automated, medical-grade | Medical devices, keypads, electronics |
Extrusion | Continuous production, pushed through a die | Cost-effective, ideal for long products | Tubing, gaskets, automotive seals |
#tssilicone #silicone #silicon #khuon #HCR #LSR #Extrusion #mold
HCR, LSR, and Extrusion